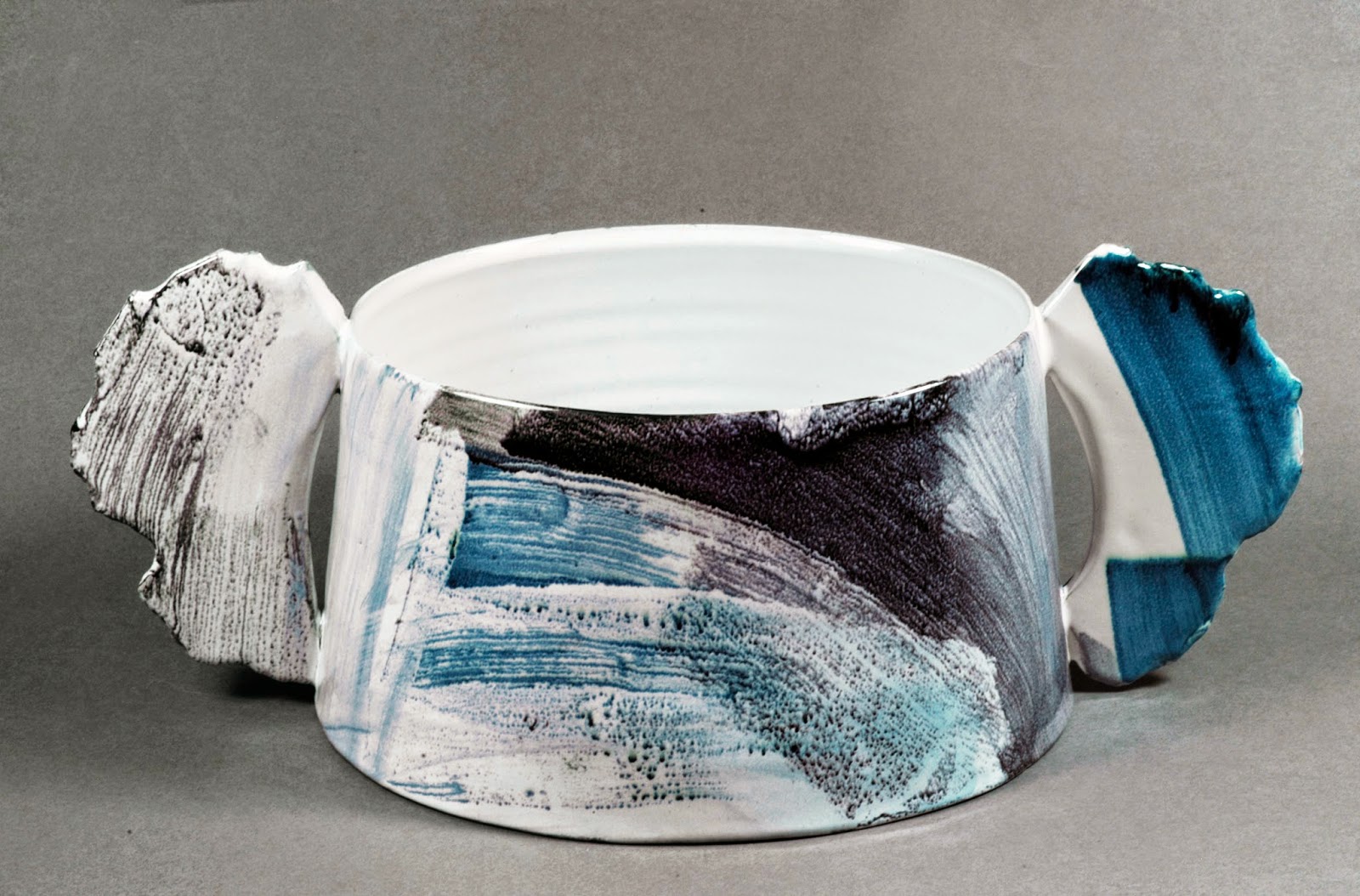
I got an e-mail in response to my post Not Quite Monochrome, asking me how to use cobalt oxide in the decoration of porcelain. As the question came from someone who declared me "the best ceramist in the world", I took some trouble over the reply. Here's an edited version of what I said.
"Cobalt blue is the most reliable and stable colouring oxide used by potters. I don’t know what it is that your potter friend has given you, but the best thing to start with is cobalt oxide, which is readily available although not cheap. Ceramic suppliers also sell blue stains, comprising cobalt oxide and other things, sometimes calcined for greater stability. Those stains have their uses, but I avoid them because I want to use washes of varying intensity, and for that the simple oxide is best. You can apply the colour as a watery wash, which gives just a hint of blue, to an intense line, which is almost black, and everything in between. Chinese brush decoration on ceramics (for example, the Qing Dynasty porcelain dish from the V&A illustrated below left) exploits this quality of cobalt oxide to great effect.
"The cobalt oxide we get today is very pure and very bright. That’s fine if you want a bright blue, but I don’t, so I tone it down. There are several ways of doing that: you can add red clay, or iron oxide, or copper oxide (which I do) or manganese dioxide. Manganese produces purplish brown, but mixed 50:50 with cobalt produces a warm black. (My piece at the head of this post uses a cobalt/copper blue and a manganese/cobalt black.) You can experiment with line blends of cobalt and another stain – say stain to cobalt in the ratios 1:9, 2:8, 3:7, 5:5, and see what is best for you.
"Cobalt is perfect on porcelain, and it doesn’t matter much whether you fire in an oxidising (clean) or reducing (smoky) atmosphere. Cobalt is stable at 1300 deg. C (cone 10), so you should have no problem at cone 5.
(I was asked what made the cobalt go fuzzy.) "If you are applying it as an underglaze stain direct on the bisque ware, and then glazing over with a clear glaze, the glaze may be disturbing your decoration, giving you a fuzzy effect. There are two ways of avoiding that. The first and simplest is to mix the oxide with a little gum Arabic dissolved in hot water. If that doesn’t work, fire the decorated bisque to about 600 deg. C before glazing.
"This is my method. I put about ½ a teaspoonful of the oxide on a shiny white tile, add a few drops of water and mix to a paste with a spatula. You can add a drop or two of gum Arabic at the same time. Then thin as required and use the tile as a palette. Some people mix in a bowl or jar, but that way you can’t vary the intensity of the wash or line so well. The addition of gum sets the oxide into a hard cake rather than a loose powder when left to dry, to be softened with water next time you use it.
"If you want the decoration to go fuzzy, you can apply it by brush as an underglaze and then rub over it with a finger. This method is even more effective if you apply the colour in-glaze, which is to say, glaze the bisque, let the glaze dry and then paint over it – which is like watercolour painting on absorbent paper. The stain will soak in and dry almost at once, then you can rub or distress it – you can even scratch through it with a pin or stick to make white lines against the blue. By the way, you can also exploit wax resist (wax emulsion, not candle wax) for a white line. By combining washes of varying intensity, rubbing with a finger, wax resist and scratching through to make a white line, you can get a wide range of decorative effects.
"Like most potters I have experience with only a small number of glazes – in fact I use only one glaze – though I believe that there will be little reaction between cobalt and any clear glaze. However, the temperature at which you fire may affect the result you get. If the glaze runs, it may carry the oxide with it. That is even more of a problem if you paint in-glaze than if you paint underglaze.
"My ceramics are earthenware, glaze fired to 1060 deg. C and I don’t know about porcelain, but there are many books with glaze recipes for you to look up. My glaze is
Lead bisilicate frit (permitted in the UK but not the USA): 56%
Cornish stone: 16%
Borax frit: 8%
China clay: 5%
Tin oxide: 7%
Zirconium silicate: 8%
"I add about 0.5% Epsom salts (magnesium sulphate) to stop the glaze settling in the bucket.
"If you are sieving a glaze you must NOT sieve it dry, which is potentially hazardous to health through the inhalation of silica dust. You should use a good quality mask when mixing the dry ingredients (a builder’s paper mask is not good enough), and you should sieve wet. To get the glaze though a 120 mesh sieve you will have to add more water than you need, sieve, then allow to settle at least 24 hrs and then pour off excess water.
"I hope that helps, and good luck in your work!"